Evaluating the Benefits and Challenges of Prefabricated Electrical Components in Construction Projects, Focusing on Cost Savings and Efficiency
The construction industry has increasingly embraced prefabrication in electrical installations as a way to improve efficiency, reduce costs, and maintain consistent quality. Prefabrication involves manufacturing electrical components off-site, allowing them to be easily assembled at the construction site. While this method offers numerous benefits, it also presents certain challenges that must be carefully evaluated to maximize its potential in various construction projects.

Benefits of Prefabrication in Electrical Installations
Cost Savings Through Labor Efficiency
One of the primary benefits of using prefabricated electrical components is the significant reduction in labor costs. Because components are manufactured in a controlled environment, there is less need for skilled labor on-site, which can result in substantial savings. In traditional electrical installations, labor costs often account for a significant portion of the total project budget. With prefabrication, tasks like cutting, bending, and assembling conduits or wiring can be completed in the factory, reducing on-site labor time by up to 30%.
Additionally, the risk of delays caused by adverse weather conditions or site-related complications is minimized, as much of the work is done off-site. This contributes to a faster turnaround and helps keep labor expenses under control.
Increased Quality and Precision
Prefabrication allows for a more controlled and consistent manufacturing process. Components are built according to precise specifications, reducing the risk of errors during installation. This level of accuracy ensures that prefabricated electrical components are of a high standard, leading to fewer quality issues during installation. As a result, contractors can expect fewer call-backs or rework, which contributes to overall cost savings.
Reduced Material Waste
Because components are prefabricated in a factory setting, materials can be measured and cut with greater precision, reducing material waste. This can lead to cost savings, as contractors purchase only the materials they need for the project, and there is less surplus or scrap. Furthermore, reduced waste aligns with sustainability initiatives, making prefabrication a greener choice for construction companies focused on reducing their environmental footprint.
Challenges of Prefabricated Electrical Components

Upfront Costs and Customization
Although prefabrication offers long-term cost savings, the initial investment can be higher due to the specialized equipment and manufacturing processes required. Construction businesses must carefully evaluate whether the savings in labor and materials will outweigh the upfront costs, particularly for smaller projects where the benefits may not be as significant.
Customization can also present challenges. Prefabricated components are built to exact specifications, so any changes to the design after the prefabrication process has begun can be costly and time-consuming. This requires detailed planning and close coordination between architects, engineers, and contractors during the design phase.
Transportation and Logistics
Transporting prefabricated electrical components from the factory to the construction site can introduce logistical complexities. Large or delicate components require careful handling, and there is always a risk of damage during transportation. Additionally, on-site storage must be managed effectively to prevent delays, especially on smaller or more congested sites where space is limited.
Cost Analysis of Prefabrication in Construction
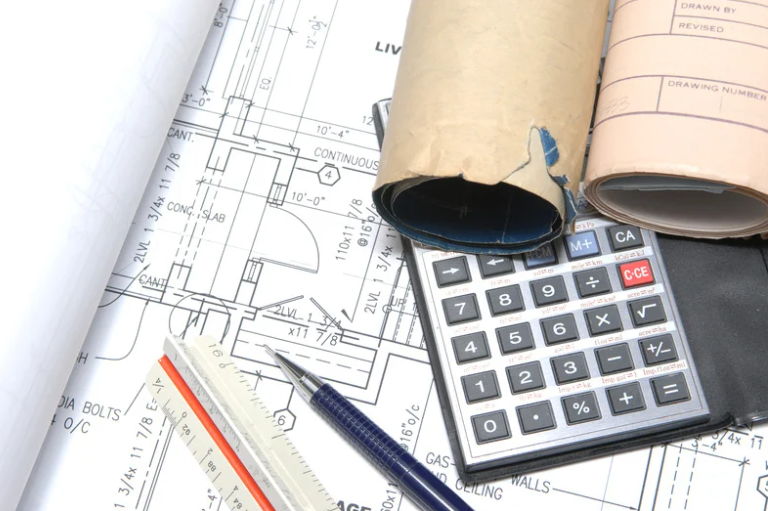
H3: Cost Breakdown for Prefabricated Electrical Installations
- Labor Savings: Prefabrication can reduce labor costs by 20-30% on average, depending on the project size. With less time spent on-site, businesses can complete more projects within the same timeframe, improving profitability.
- Material Costs: While the cost of prefabricated components may be slightly higher than traditional materials due to factory overhead, this is often offset by reduced waste and increased efficiency during installation.
- Transportation Costs: Depending on the distance between the factory and the construction site, transportation can account for an additional 5-10% of the total project cost. However, this cost is usually outweighed by the savings in labor and material waste.
- Upfront Investment: Businesses may need to invest in specialized equipment or training for workers to handle prefabricated components, which can increase upfront costs. However, this investment often pays off in long-term efficiency gains.
When to Call a Professional
Prefabrication in electrical installations requires a high level of expertise and careful planning. It’s essential to collaborate with experienced electrical contractors who understand the intricacies of prefabricated systems. A professional can:
- Ensure Compliance with Local Codes: Electrical installations must comply with local safety regulations and building codes. A professional contractor will ensure that all prefabricated components meet the necessary standards.
- Design Coordination: Prefabrication requires detailed planning and coordination with other trades, such as plumbing and HVAC, to ensure that all systems integrate seamlessly on-site. Professionals are skilled in managing this process to avoid costly design conflicts or delays.
- Address Complex Installations: In projects with complex electrical systems or custom requirements, working with an expert ensures that all components are installed correctly and perform optimally.
The Future of Prefabrication in Electrical Installations
The use of prefabricated electrical components in construction projects is gaining traction due to the significant cost savings, improved efficiency, and high-quality results it offers. However, the challenges—such as upfront investment and logistical considerations—must be carefully managed to fully capitalize on the benefits. As technology and manufacturing techniques continue to advance, prefabrication is likely to play an increasingly important role in the future of electrical installations, particularly in large-scale projects. Construction businesses should consider consulting with industry experts to assess the viability of prefabrication for their specific projects and ensure that installations are completed smoothly and efficiently.