The Importance of Safety in Electrical Work
Electrical work is one of the most hazardous trades in the construction industry. The risks associated with electrical work include electric shocks, burns, falls, and even fatal accidents. To mitigate these dangers, it is essential to follow strict safety standards and best practices. These protocols ensure the safety of electricians and other workers on job sites, while also ensuring compliance with legal regulations. This comprehensive overview will cover the latest safety standards, advancements in Personal Protective Equipment (PPE), and best practices for reducing risks on electrical job sites.
Current Safety Regulations in Electrical Work
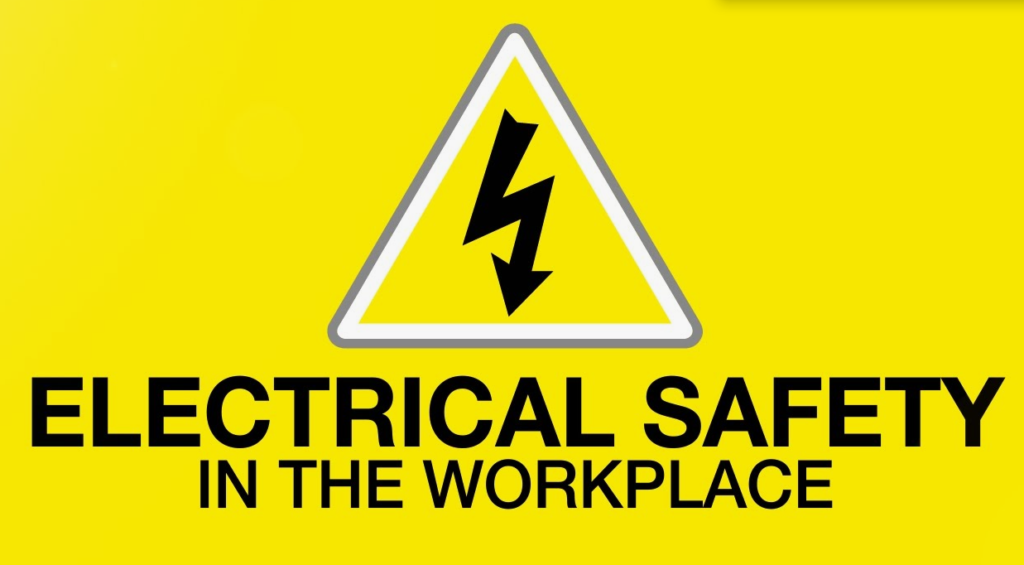
Electrical safety is governed by a variety of national and international standards and codes that set minimum requirements for safety practices. Following these regulations is not only critical for worker safety but also for ensuring that all electrical installations meet legal and technical standards.
OSHA Standards and Compliance
In the United States, the Occupational Safety and Health Administration (OSHA) sets forth the primary regulations that govern electrical safety in workplaces. OSHA mandates that all employers ensure a safe working environment, which includes maintaining electrical systems and enforcing the use of proper PPE.
Key OSHA regulations for electrical safety include:
- Lockout/Tagout Procedures (29 CFR 1910.147): These procedures prevent the accidental energization of electrical systems during maintenance.
- Electrical Safety-Related Work Practices (29 CFR 1910.331–335): This standard includes specific requirements for working with or near electrical systems, including hazard identification and PPE requirements.
- Hazardous Energy Control (29 CFR 1910.333): This regulation addresses safe practices for servicing and maintaining electrical systems, including the use of electrical isolation devices.
National Electrical Code (NEC)
The National Electrical Code (NEC) establishes safety guidelines for electrical installations in residential, commercial, and industrial settings. The NEC ensures that all electrical systems are designed, installed, and maintained in a way that minimizes the risk of electric shock, fire, and other electrical hazards. Key areas of the NEC relevant to safety include:
- Grounding and Bonding Requirements
- Overcurrent Protection
- Arc-Fault and Ground-Fault Circuit Interrupters (AFCIs and GFCIs)
- Safe Electrical Design and Installation
Adherence to NEC guidelines is essential for both compliance and safety in electrical projects.
PPE Advancements in Electrical Work
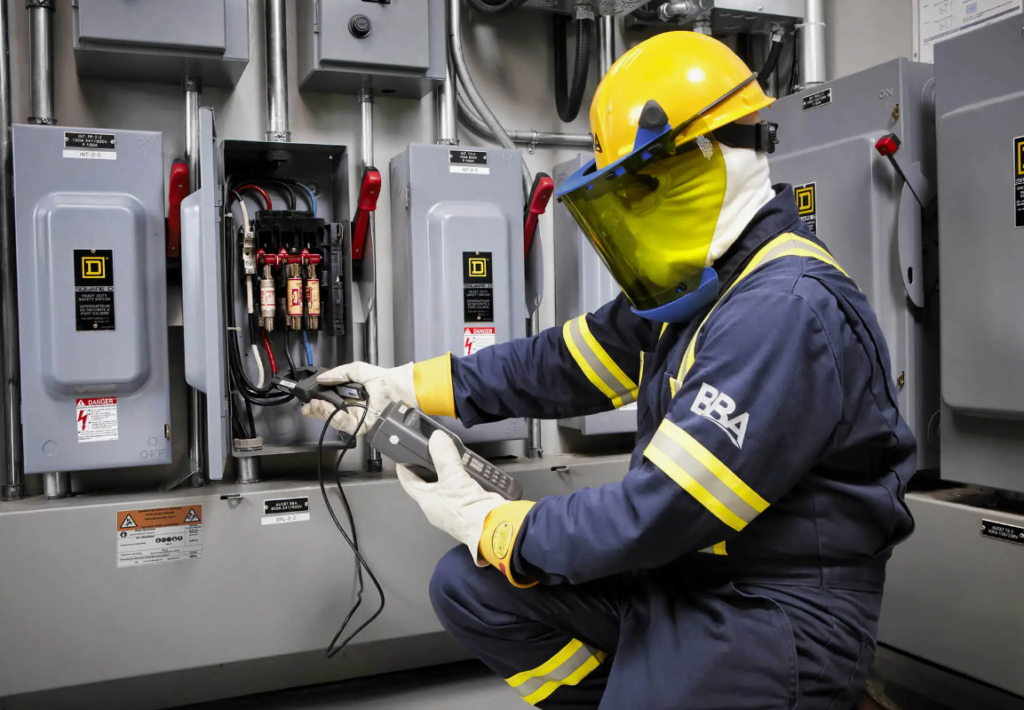
Personal Protective Equipment (PPE) plays a critical role in protecting workers from electrical hazards. Over the years, advancements in PPE technology have provided greater protection, comfort, and durability for electrical workers.
Arc-Rated Clothing and Gloves
Arc-rated clothing is designed to protect workers from the intense heat generated by electrical arc flashes. Modern arc-rated fabrics are lightweight, breathable, and flame-resistant, providing both safety and comfort. Proper arc-rated gloves are equally important, offering insulation and protection from high-voltage equipment.
Cost considerations: High-quality arc-rated clothing and gloves can range from $150 to $500, depending on the level of protection and customization required for a specific job.
Insulated Tools and Equipment
Electrical workers often rely on insulated tools that are specifically designed to protect them from electric shocks. Insulated screwdrivers, pliers, and testers are among the most commonly used tools in electrical work. These tools must meet strict safety standards and be tested regularly for insulation integrity.
Insulated tools can range in price from $20 to $150 per tool, depending on the quality and voltage rating.
Head, Eye, and Hearing Protection
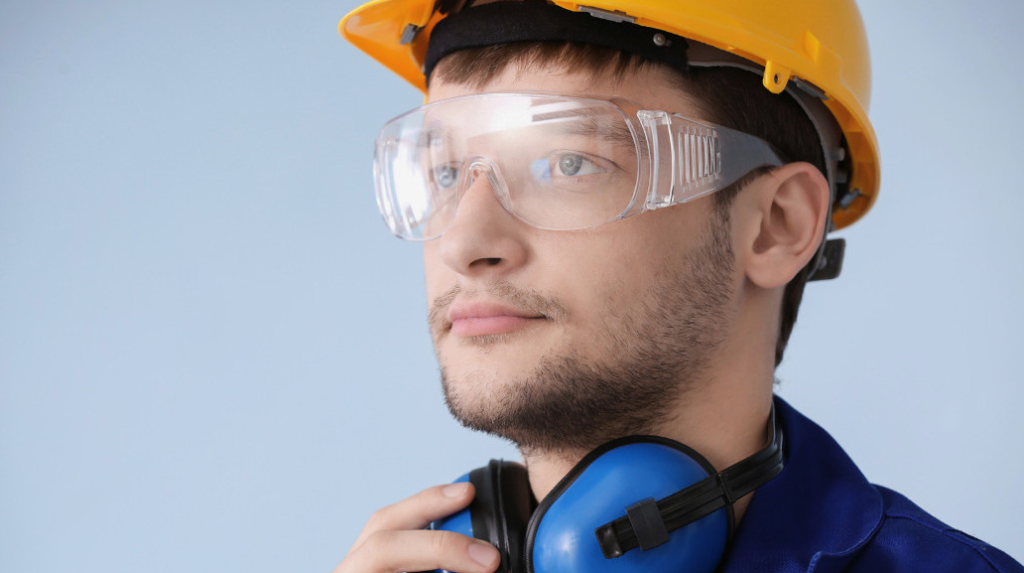
Advancements in head, eye, and hearing protection ensure that electricians are shielded from flying debris, loud noises, and potential impact injuries. Modern safety helmets now feature built-in visors and attachable earmuffs, providing comprehensive protection.
The cost of a high-quality safety helmet with integrated features typically ranges between $75 to $200.
Best Practices for Reducing Risks in Electrical Work
Adopting best practices is essential for minimizing the risks associated with electrical work. These practices go beyond compliance with regulations and emphasize proactive measures that keep job sites safe.
Regular Safety Training and Certification
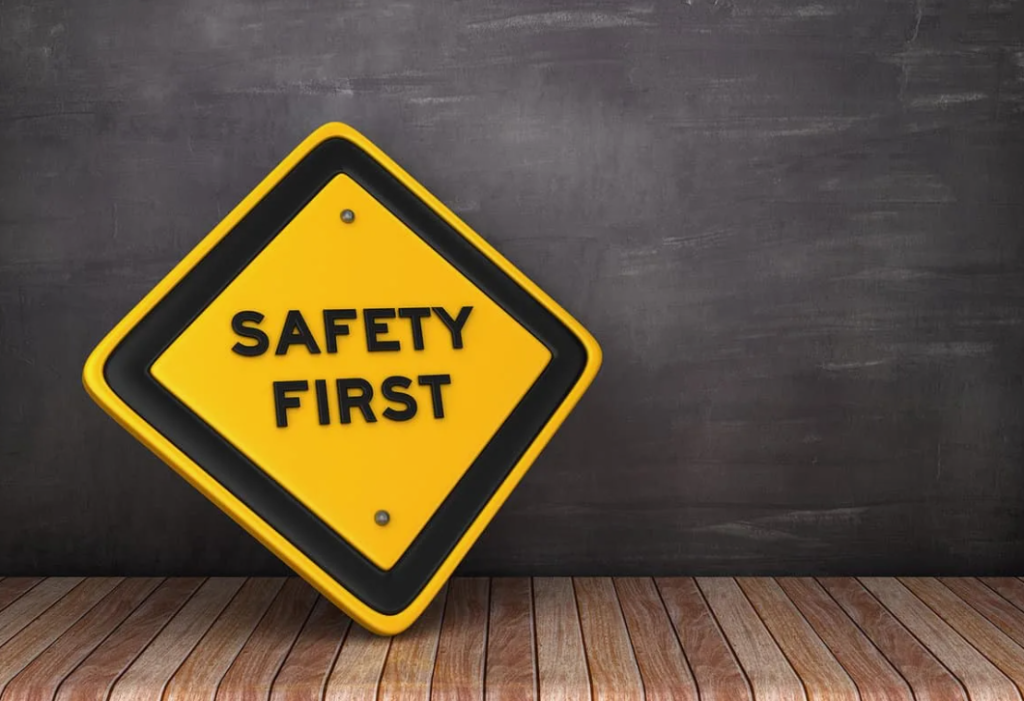
Ensuring that all workers are properly trained in electrical safety is critical. This includes comprehensive training on how to recognize and avoid hazards, proper use of PPE, and emergency procedures. Additionally, workers should stay updated with certification programs to ensure they are compliant with the latest safety standards.
Training costs can range from $300 to $1,200 per worker, depending on the level of certification required.
Conducting Job Hazard Analysis (JHA)
A Job Hazard Analysis (JHA) is a systematic process that identifies potential hazards associated with electrical tasks and helps establish safe procedures. Conducting JHAs before starting any electrical work ensures that all risks are assessed, and necessary precautions are taken.
Establishing Lockout/Tagout Procedures
Lockout/Tagout (LOTO) is one of the most important safety protocols in electrical work. Proper implementation of LOTO procedures ensures that machinery and electrical systems are completely de-energized before any maintenance work begins. LOTO procedures prevent accidental energy release, which could result in severe injury or death.
When to Call a Professional Electrical Safety Expert
Some electrical projects require expert-level knowledge to ensure safety and compliance with all relevant standards. Here are situations when calling in a professional is essential:
- Complex Electrical Systems: If a project involves high-voltage systems or complex electrical setups, it’s critical to consult with an experienced electrician or electrical engineer. They can assess the system for potential hazards and design safe solutions.
- Safety Audits and Inspections: Hiring a professional for safety audits ensures that all systems meet OSHA, NEC, and other local safety requirements. These audits can identify any weaknesses in electrical safety practices and help avoid costly fines or accidents.
- Training and Certification: For specialized training or high-risk jobs, calling an expert to provide on-site safety training ensures that all workers are prepared and certified to handle complex electrical tasks.
The Future of Electrical Safety Practices
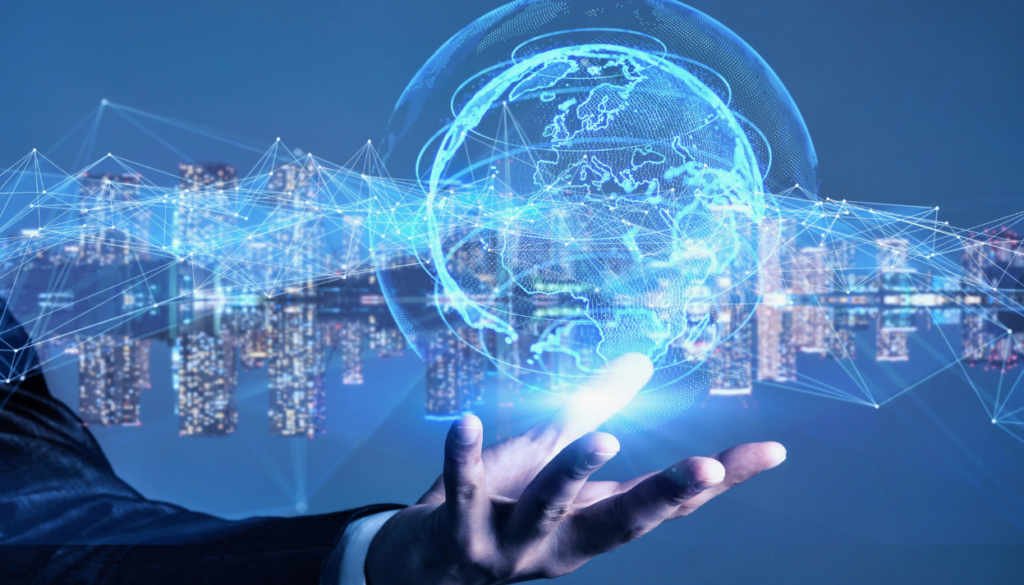
With the rise of smart technologies, renewable energy systems, and more complex electrical infrastructures, the future of electrical safety will continue to evolve. Automation and digital tools will likely play a larger role in monitoring electrical systems, detecting hazards, and ensuring compliance with safety standards. Additionally, further advancements in PPE and tools will provide even greater protection for electricians.
Construction businesses and electrical contractors must stay up-to-date with the latest safety standards and invest in ongoing training to ensure their teams are well-equipped to handle modern electrical challenges. Consulting with professionals and adhering to established best practices will help to reduce risks and create safer working environments for everyone involved.